Thermal treatments, and their application in raw materials and feed concentrates optimizes their utilization, providing better nutritional and performance results in animals.
These thermal treatments also allow the use of proximity raw materials, which would be impossible under any other circumstance or process. This allows the combination of these locally obtained ingredients with other raw materials,strengthening the concept of circular economy. In today’s constant search for efficient and sustainable production systems, where feeding programs are adjusted to each phase of the production cycle, it is necessary to consider and work with degradation values and speeds.
Main thermal treatments
We can divide heat treatments into 2 large groups:
- Dry: heated, dried and roasted.
-
Wet: heat and moisture (conditioning, cooking, granulation, expansion and extrusion).
- Conditioning: Application of thermal treatments without producing changes to the physical format of the ingredient. It consists of heating the feed, generally through indirect heat. Its main objective is to sanitize, reduce or eliminate microorganisms, while facilitating a subsequent granulation process.
- Cooking and roller milling: Flakes are obtained through steam cooking at an approximate temperature of 100 ° C for periods between 40 and 60 minutes. These are then subjected to roller mills,where the drying takes place.
- Granulation: It is the most used process in feed mills. The trend in recent years is to shift towards a higher percentage of granulated and crumb feed in its different sizes. In this process, feed found in meal form, is transformed into granules (pellets) with different diameter and length. Achieving a final product with two fundamental properties: hardness and durability.
- Expansion: This process uses temperatures ranging from 90°C and 120°C and lower pressure values than extrusion. It is also used to treat, and expand individual or combined products such as: corn, soybeans, wheat, cakes, etc.
- Extrusion: It is considered as the most complex process and it employs the different variables with greater intensity. It is carried through the use of an extruder composed by one or two bodies. Raw materials are previously conditioned with the addition of liquids and steam before being subjected to the action of the extruder. The process occurs under conditions of high pressure and temperature values, ranging from 120°C and 170°C; exiting through a matrix where the highest pressure is applied.
Wet or humid thermal treatments can be performed through five different processes. The working conditions for these processes are shown in Table 1.
Table 1. Working conditions of the different thermal treatments
Adjustable variables in thermal treatments for animal feed
Working conditions can be modulated according to variables and the combinations between them (Figure 1). They will basically depend on: the type of raw material or feed, the objectives that been established, and the type of animal for which that feed is intended. These can also include the industrial capabilities of each operator.
Figure 1. Adjustable variables in thermal treatments.
Main objectives of thermal treatments
Physical modification of feed:
Transform feed into meal and granules of various formats. It facilitates intake, making feed more attractive, and in turn generating less waste.
Modify nutrients through a bromatological and chemical standpoint:
Allow an adequate formation of the granules which confers them stability and improves their digestibility. Seeking three main objectives:
- Gelatinization of starch.
- Plasticization of particles: Fundamental to establish strong bonds between the particles.
- Permeability of cell walls: Facilitates the penetration and action of digestive juices.
Reduce/eliminate microorganisms:
Specifications regarding acceptable limits for microorganism levels in feedstuffs.
Salmonella: Absence in 25 g
E. Coli: Absence in 1 g
Fungi: Less than 104 cfu/g
Clostridium: Less than 100 cfu/g
Enterobacteriaceae in Grain Feed/Sanitized Feed: Less than 100 cfu/g
Enterobacteriaceae in Meal Feed: Less than 105 cfu/g
Major impacts of thermal treatments on feed
Nutrients
The structural changes which occur in nutrients according to the type of treatment to which they are subjected to are detailed below. These can also be compared in Table 2.
In general, starch tends to improve digestibility under the recommended limits for the use of heat treatment variables and as these intensify.
Protein improves to a certain extent, and then stabilizes when subjected to heat treatment. If the treatment continues, the risk of denaturation increases significantly.
Vitamins, enzymes and other supplements are lost during the early stages of such treatments. This loss tends to be greater as the employed variables intensify. The damages and losses depend on the sensitivity and protection of these compounds.
Table 2. Speed and structural changes according to the type of thermal treatment that is applied.
Microbiology: Reduction/Elimination
As a general rule: A more intense use of variables, results in a greater reduction of microorganisms.
A period of 40 seconds is generally sufficient to eliminate all the microorganisms that pose the biggest health threats. This is especially especially true for salmonella. Nonetheless, it is worth noting that this is true when the temperature remains above 80ºC and the humidity provided through steam is at least 3%.
GRANULATION
Granulation is a mechanical process that converts a mixture of ground raw materials into grains. This process is usually carried out in a granulator with the previous inclusion of steam, followed by a subsequent cooling phase where temperature and humidity are lost. Obtaining cylindrical particles with a higher density.
Some of the processes that take place before granulation, are:
grinding of raw materials (pre-milling or grinding factory).
mixing of raw materials to achieve a homogeneous mixture.
conditioning (kneading with moisture and heat to produce a plastic and lubricated mass).
previous compression through a matrix which allows to obtain a certain size and shape of granulation.
screening to remove fine particles.
the final phase includes air drying and cooling.
The feed must be fluidized within the conditioner and it must be well mixed with the steam. In order to achieve this, the shovels must move the feed evenly through the well-sized conditioners.

Advantages of granulation:
- Improves animals’ productive yield.
- Higher microbiological hygiene in relation to meal feeds.
- Reduction of transport costs.
- Improvement of digestibility, through the gelatinization of starch.
- Elimination of anti-nutritional factors found in some vegetable raw materials.
- It allows the use of more solid raw materials. As well as the combination of other raw materials and liquid additives.
- It allows the use of less palatable raw materials.
The parameters for measuring the quality of granules are:
Durability:
It is a parameter used for the physical analysis of the feed. It evaluates the amount of fine particles which still preserve their cover after having been subjected to mechanical or pneumatic agitation. This assessment aims to simulate the transport and handling conditions of pellets under normal circumstances within the feed mill. This parameter is expressed as a percentage.
The level of fat will mark the durability. Hence, the granules which are intended for beef cattle consumption, can take a value of 97% or higher as a reference and optimal point.
Hardness:
It is defined as the amount of force it takes to break a pellet or a series of pellets at the same time. This parameter is expressed in Kg/cm2.
Water activity:
It measures the amount of free water left after cooling within the grain. Free water is water not linked to nutrients or structures. Therefore, its presence promotes the growth of fungi and bacteria,as well as the onset of oxidative processes and the appearance of insects. Water activity is measured within a range from 0 to 1 aw (water activity).
Thus, an optimal reference value for feed should be close to 0.65 to w, and should never exceed the 0.7 aw mark.
Fine particle percentage:
It depends on where the sample is taken, but the reference value for robot obtained feed should be less than 3%.
Starch gelatinization:
It is the best and cheapest binder, since it not only provides binding strength, but also elasticity, which contributes to improved durability. Gelatinization is normally achieved at 60ºC (Table 3) and with 3% free water.
Table 3. Gelatinization temperature of cereal starch.
1 Polysaccharide constituent of starch, formed by glucose molecules.
Wheat is considered as the best cereal for granulation due to its low fat content and the low temperatures that it requires for starch gelatinization.
The raw material parameters evaluated for granulation are shown in Table 4, where the values of wheat can be compared with those of other cereals.
Table 4. Raw materials and their value according to their potential use for granulation.
In the second part of this section, we will delve into extrusion and its effects on the ingredients used for ruminant diets.
Conclusions 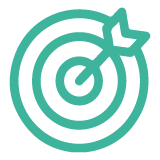
The application of thermal treatments on raw materials used in ruminant feed, can:
- Maximize the digestibility of starch within the ration, while maintaining the fiber effect, reducing the fraction of non-degradable rumen starch, and increasing the efficiency of amylolytic microflora in the rumen.
- Improve the synthesis of milk protein, by increasing the amount of digestible protein within the intestine.
- Improve the microbiological quality of products.
It is also worth noting that:
- We must analyze the carbon footprint and sustainability associated with the use of different thermal treatments. As well as looking into the returns obtained after the initial investments made on these processing methods.
- The current and future scenario of beef cattle requires the presence of well-granulated feed to achieve success. This is also true for dairy production, and even more so in robotic milking systems. Therefore, the quality of the granules, as well as its organoleptic properties such as smell, taste and texture must be carefully safeguarded.
You may also like to read: “Importance of thermal processing of soybean meal for poultry nutrition.”